The customer
The Flight Operations department of the German Aerospace Centre (DLR) in Braunschweig tests new developments on and inside aircraft under actual conditions. Tasks includes aerodynamic studies, in-flight simulators as well as the testing of navigation systems and air traffic management systems. Research commissions come from within the DLR itself as well as externally from universities, national authorities, industry and research institutes. The six aircraft and two helicopters undergo preparation, often lasting several weeks, with modifications and new component installation to cater for the requirements of the relevant research contract. Testing in the air takes place only after completion of extensive ground tests. The main platform for conducting the research is a more than 20-year old VFW 614 ATTAS (Advanced Technologies Testing Aircraft System). For more than two decades it has been flying throughout Europe on DLR test contracts.
THE TASK
A height-adjustable working platform had to be constructed for work on the vertical stabilisers of the VFW 614 ATTAS which are around eight metres high. The required size of the platform was determined by two factors: the width of the horizontal stabilisers which need to fit below the working platform; and the need for a free-standing projection of at least 1 m. A particularly high load-bearing capacity was required: in addition to two technicians, materials and spare parts also need to be accommodated on the working platform. Lightweight was also required to enable easy movement by two people. This was then a challenging specification that the DLR set us.
THE SOLUTION
In close collaboration with the DLR, ZARGES Aluminium Systems GmbH (ZAS) developed a concept that would meet the difficult and sometimes conflicting requirements. Many discussions with everyone involved in the project were necessary before agreeing the best result – especially concerning the equipment’s height adjustment. “This was one of the most important prerequisites to enable us to easily carry out work on the vertical stabilisers”,explained Stefan Schröder, responsible at DLR for research contracts as well as for technical support in the aircraft hangar. The ZARGES height-adjustable working platform replaced the rigid scaffolding previously used, thus considerably simplifying the work. The height of the 2.20 m x 4.50 m platform can be varied between 3.50 and 7.00 metres. Maximum load capability has been increased to 300 kilograms so that two people and a wide range of materials can be accommodated on the platform. Development engineers and technicians can now carry out work easily and safely on the vertical stabilisers of the ATTAS aircraft.
“ZARGES has met the challenging specifications exactly to our needs.”
Stefan Schröder, DLR
Technical features of the work platform
Height adjustment.
- Multi-level adjustment between 3,50 m and 7,00 m.
- Notches every 50 cm.
- Height-adjustable by manual crank with relevant gear ratio.
- Specially developed guide profiles which simultaneous increase stability.
Weight:
- As lightweight as possible was one of the important criteria in the design specification.
- Easily operated by two people.
- Empty weight of 1260 kg with a load capacity of 300 kg. (Only 40 % of the weight of a steel construction)
Large platform with high load capability and 1.00 metre projection:
- Particularly large working platform (2,20 m x 4,50 m) featuring ample space for spares and tooling.
- Approx. 1.00 m unencumbered projection for maximum possible reach.
- Optimum tilt safety assured due to a broad crossbeam underneath the aircraft.
INTERVIEW WITH STEFAN SCHRÖDER, DLR PROJECT LEADER
ZARGES: | What factors made the acquisition of a new working platform for the research aircraft necessary? |
Stefan Schröder: | We had been using rigid scaffolding for work on the lateral stabilisers of our VFW 614 ATTAS but it was no longer meeting our needs. For example, the height of the scaffolding could not be adjusted and access was not possible to every area of the vertical stabilisers. |
ZARGES: | Height adjustability was therefore one of the most important points? |
Stefan Schröder: | This was definitely an important factor for us. The width of the new working platform enables it to be positioned over the horizontal stabilisers and then the height adjusted stepwise from 3.50 to 7.00 m. It was also important for the work platform to have a high payload because it needs to accommodate material as well two employees. But we also needed the platform to be as lightweight as possible to enable easy manoeuvrability by two employees. |
ZARGES: | How did the collaboration with ZARGES come about? |
Stefan Schröder: | We were already familiar with ZARGES from many other projects and work platforms that we are using on our aircraft We knew ZARGES to be a good partner for such special constructions, both in terms of project planning and implementation. The team always managed to find, in close cooperation with us, optimal solutions for our exacting needs. |
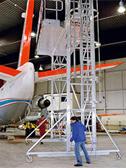
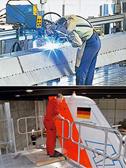
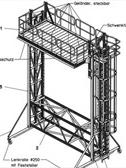
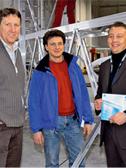
We are available to answer your queries on ZARGES work platforms.
By telephone to the customer centre for access technology on +49-(0)881-687-100 or via our contact form.